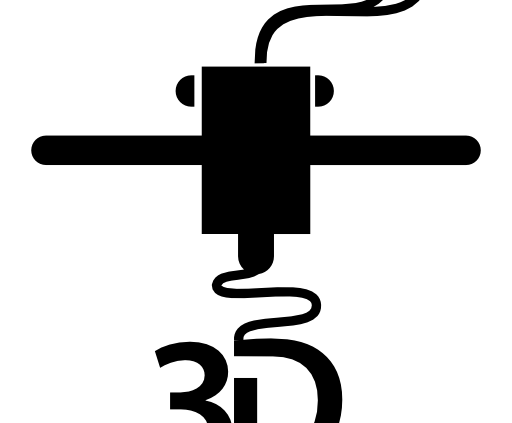
در این مقاله می خواهیم مشکلات رایج در پرینت سه بعدی را بررسی کنیم و راه حل هایی را برای رفع آن ها معرفی کنیم.
در صورتی که از پرینتر سه بعدی آشنایی کافی ندارید می توانید مقاله نگاهی کوتاه به سیر پیشرفت پیرینتر سه بعدی در این چند سال اخیر را مطالعه کنید.
برای در خواست پرینت سه بعدی اینجا کلیک کنید.
در ادامه با خواندن مطالب شما احتمالا اکثر مشکلات موجود در پرینت سه بعدی را می توانید شناسایی و با روش هایی که معرفی شده است. اصلاح کنید.
مشکلات رایج در پرینت سه بعدی
- تراوش کردن : این حالت معمولا برای فیلامنت های نازک در فضای خالی بین دو قسمت مختلف ایجاد شده اند به وجود می آید.
راه حل : برای جلوگیری از این مشکل می توانید سرعت حرکت سر پرینت را افزایش داده یا مسیر حرکت را طولانی تر کنید . دمای اکستروژن را کاهش دهید.
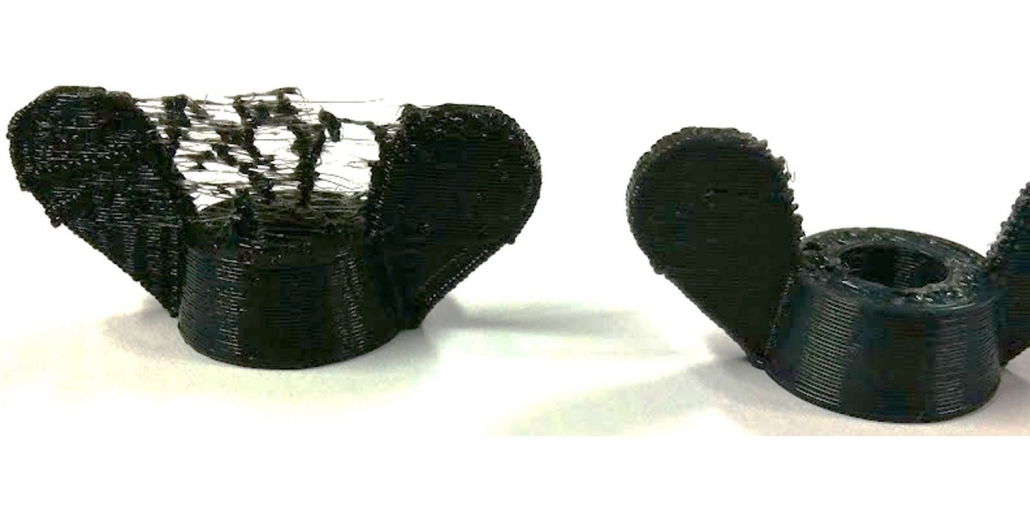
2.برآمدگی: این حالت برای سطوح آویزان اتفاق می افتد و شکم می دهند. زیرا عملیات سرد شدن به آهستگی اتفاق می افتد و تغییر شکل می دهد.
راه حل: با استفاده از دستگاه تهویه و یا فن باید قطعه را سریع سرد کرد.
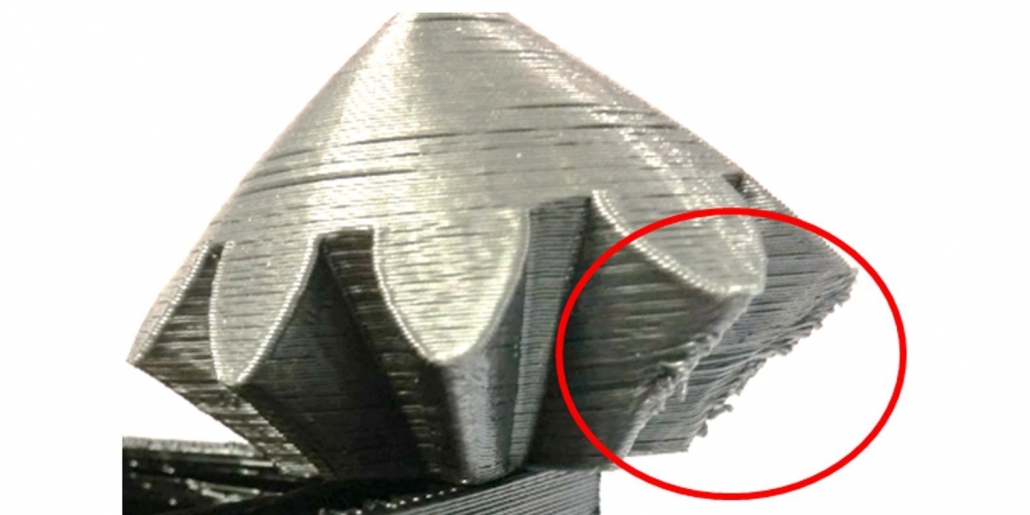
3. ورقه ورقه شدن : لایه ها به خوبی به یکدیگر نچسبیده و از هم جدا قرار می گیرند.
علت : عدم وجود سطح اتکای مناسب برای لایه هاست. دمای اکستروژن بسیار پایین است و قبل از آن که لایه ها به هم بچسبند سرد می شود. یا ممکن است چیزی در نازل مانع خروج کامل مواد شده باشد.
راه حل: کالیبره کردن سرعت پاشش ماده با حرکت آن – تمیز کردن یا تعویض نازل – افزایش دمای اکستروژن – افزایش هم پوشانی لایه ها – افزایش هم پوشانی لایه ها
ورقه شدن ورقه شدن الیاف
4. کمبود ماده اولیه برای قطعه: ممکن است به علت نازک بودن برخی دیواره ها و لایه ها یا سر خوردن و لغزیدن لایه ها، قطعه تخریب شود.
راه حل: کاهش سرعت و طول برگشت پرینت – افزایش طول اضافه برگشت در نرم افزار اسلایسر – افزایش فشار سوزن پرینت
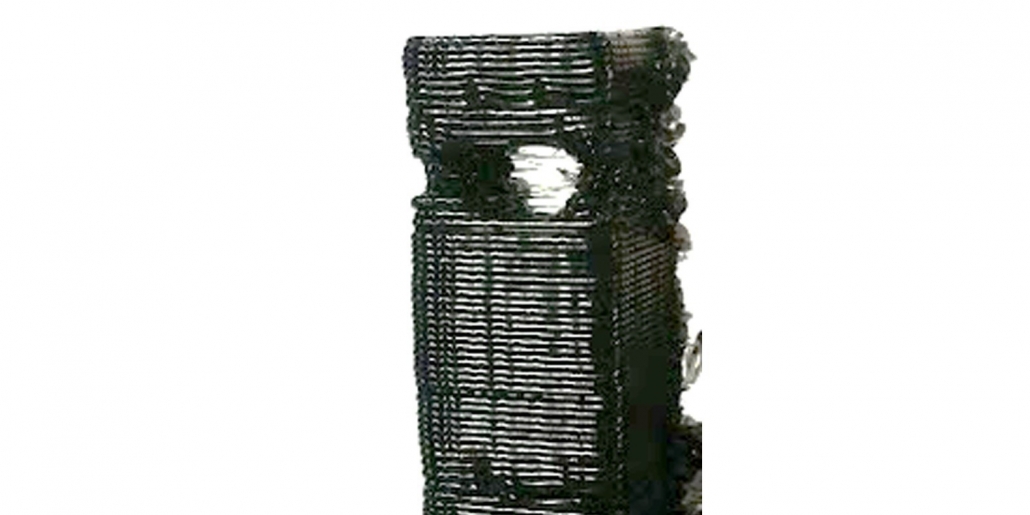
5. گوله شدن: به وجود آمدن سطوح برآمده مانند تاول در مناطقی که سطح کوچکی دارند.
علت: آن عموما دمای بالای اکستروژن و یا دیر سرد شدن فیلامنت ها می باشد.
راه حل: سرعت سرد شدن قطعه را افزایش دهید یا سرعت پرینت را کاهش دهید.
تاول زدن قطعه در اثر حرارت زیاد تاول زدن در اثر دیر سرد شدن
6. جدا شدن دیواره های نازک: لایه های دیواره های نازک از هم جدا شده و فاصله ای میان آن ها خالی می ماند.
علت: این مشکل نازک بودن بیش از اندازه دیواره است.
راه حل: می توان با افزایش قطر دیواره یا انتخاب نازل کوچک تر این مشکل را حل کرد.
دو لایه شدن دیواره ایجاد شکاف بر روی دیواره
7. حرکت افقی یک لایه: یک لایه در محور x یا y جا به جا می شود.
علت: آن ممکن است جا به جا شدن پرینتر یا سر پرینتر یا کفی آن باشد.
راه حل: شتاب حرکت در راستایی که این مشکل به وجود می آید را کاهش دهید.
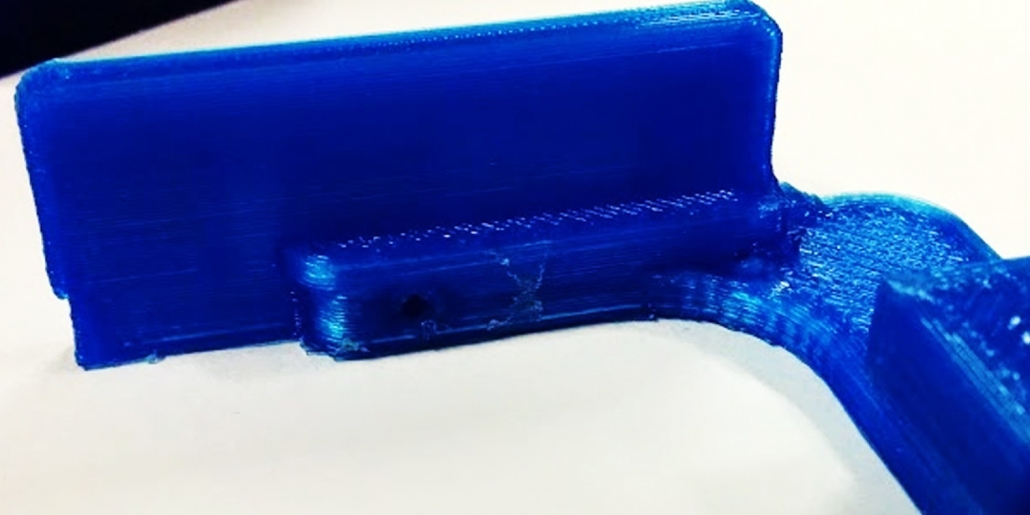
8. جا به جایی برابر لایه ها: لایه ها به اندازه مساوی جا به جا می شوند.
علت: عدم جابه جایی سر پرینتر یا پلات به علت گرمای بیش از حد موتور ها
راه حل: خنک کردن موتور ها (استفاده از فن)
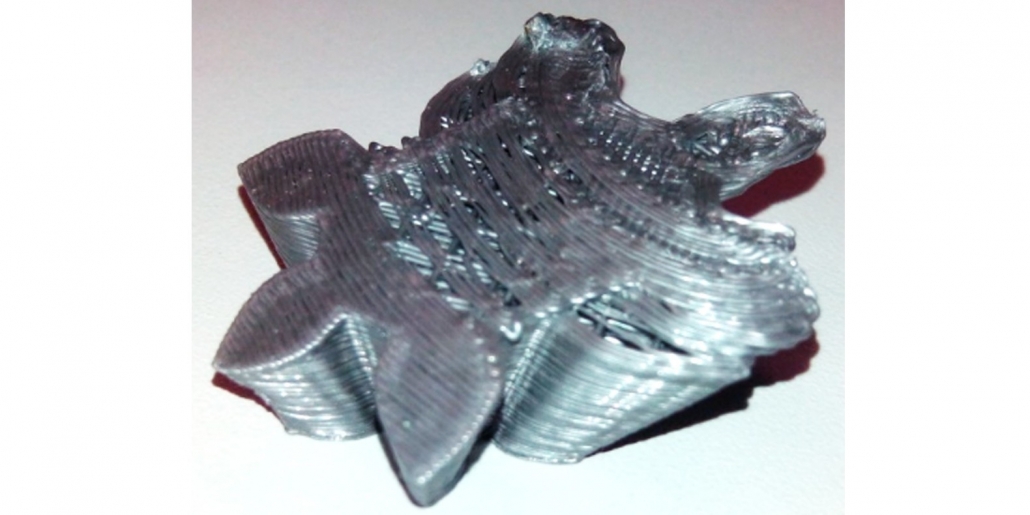
9. گوشه ها خم می شوند: قسمت هایی از گوشه ها که بیشتر حالت آویزان دارند خم می شوند.
علت: آن عموما اختلاف دمای لایه ها و آویزان بودن بیش از حد می باشد.
راه حل: می توان با خنک کاری یا کاهش آویزان بودن این مشکل را حل کرد.
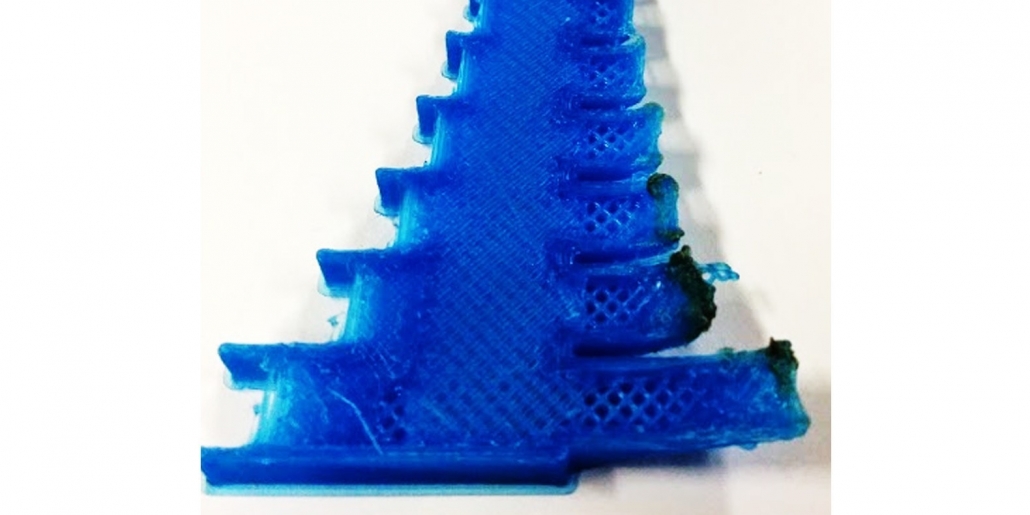
10. تاب ور داشتن : گوشه های قطعه پرینت از سینی جدا شده و قطعه تاب بر می دارد.
علت: عدم چسبندگی کافی به سینی – بیش از اندازه بودن ضریب انقباض پذیری – لایه اول به درستی بر روی بورد قرار نگرفته باشد.
راه حل: عوض کردن ماده پرینت ( می توان از PLA ها استفاده کرد.) – چسب زدن به سینی پرینت – تنظیم کردن ارتفاع سینی و صاف بودن آن – ابتدا یک لایه نازک بریزید تا پوششی برای الیاف بعدی باشد و به خوبی بچسبند. – یک لبه به زیر لایه اضافه کنید. سینی پرینت را گرم کنید. – سطح سینی را کاملا تمیز و خشک کنید. – استراتژی پر کردن را تغییر دهید و از مدل لانه زنبوری استفاده کنید.
تراکم داخلی را کاهش دهید.
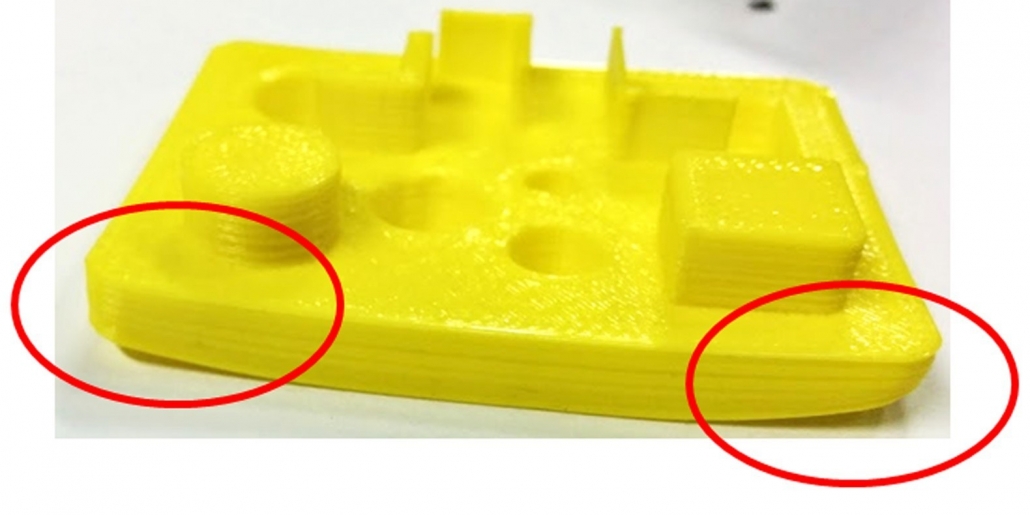
11. تراکم بسیار کم است: تراکم قطعه اشتباه است.
علت : نرخ جریان پرینت کم است.
راه حل: تعویض نازل – مشکل در تزریق سیم پرینت – کثیف یا مسدود شدن مسیر اکسترود
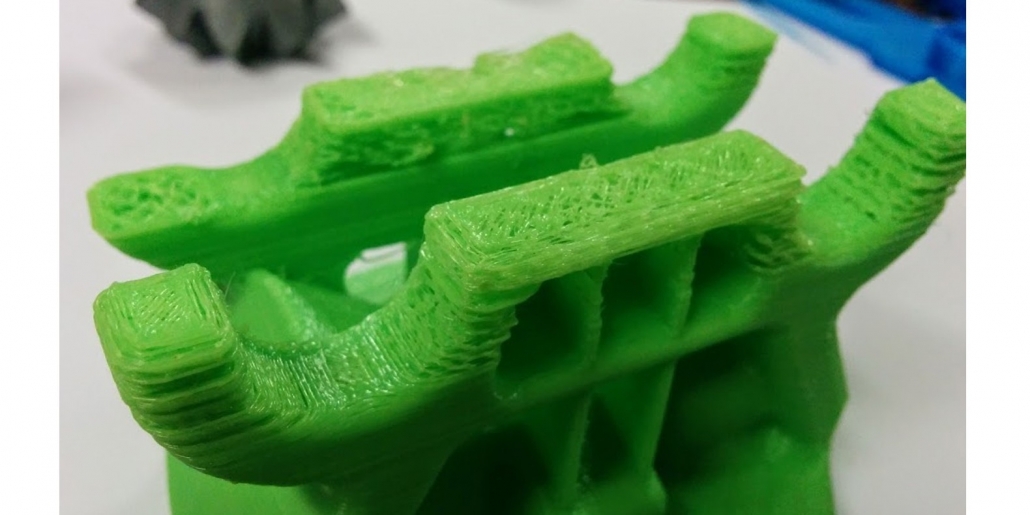
12. گوشه ها به درستی ساخته نمی شوند. گوشه ها به اندازه کافی صاف نبوده و بیرون زده اند.
علت: حرکت بسیار کند نازل از این مناطق باعث انباشته شودن ماده اضافه در گوشه ها می شود.
راه حل: گوشه ها را در مدل ساخته شده فیلت بزنید. – افزایش جرک محور کنترل پرینت سه بعدی
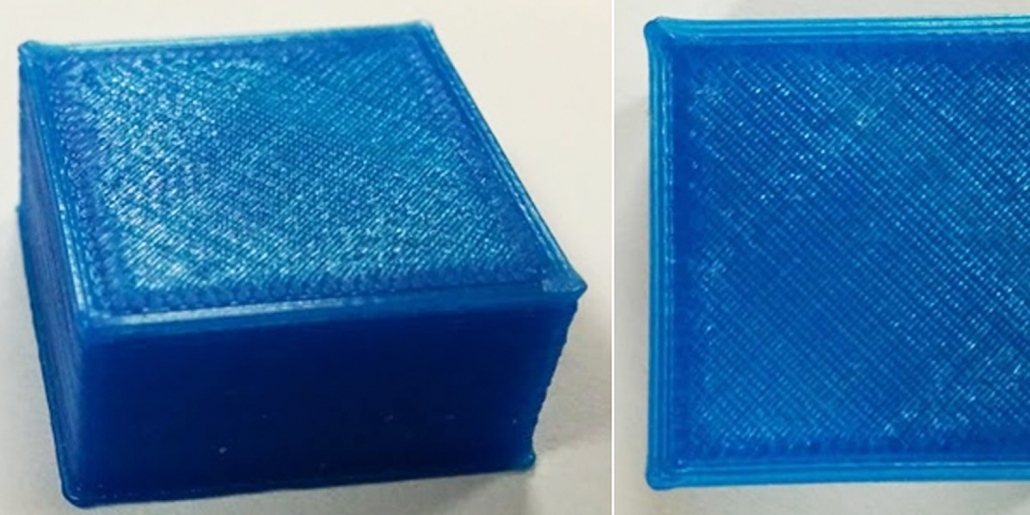
13. قطره های سیاه : قسمت هایی از ماده (PLA یا ABS) می سوزد و قطرات سیاه به وجود می آید.
علت: آب بندی نادرست نازل باعث می شود تا مقدار از ماده نشت کرده و بسوزد و بریزد.
راه حل: بازکردن نازل و آب بندی مجدد
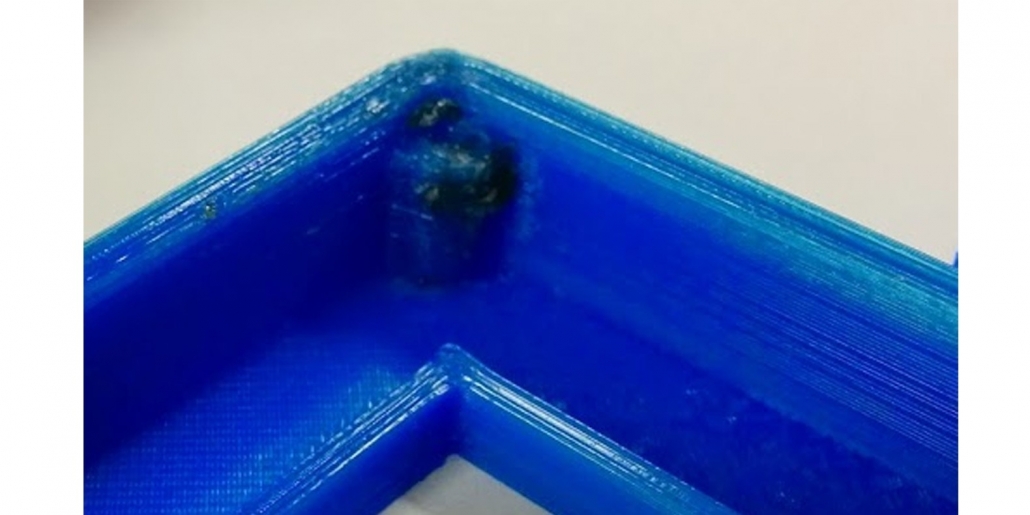
14. عدم جوش خوردن لایه ها: در برخی قسمت ها شکننده است و لایه ها کامل به هم نچسبیده اند.
علت: سرد شدن سریع پرینت و تاخیر در ریختن لایه جدید
راه حل: کاهش نرخ سرد شدن قطعه – افزایش سرعت پرینت لایه ها
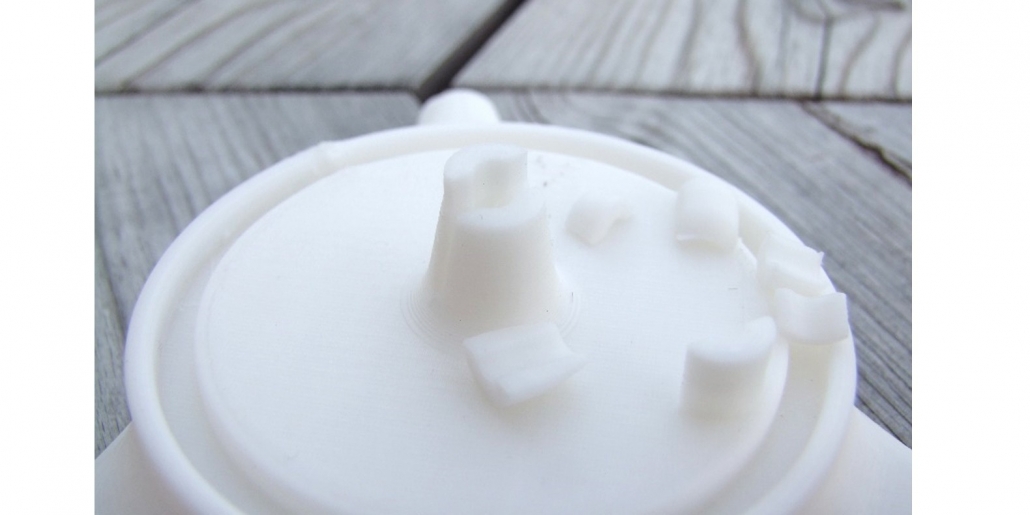
15. وجود حباب در لایه ی اول
علت: حضور ماده مرطوب که با تماس با صفحه داخ باعث ایجاد بخار و حباب می شود.
دمای سینی برای ماده مورد نظر مناسب نبوده است.
راه حل: مواد اولیه در مکانی خشک یا در حضور رطوبت گیر ها بسته بندی کنید.
موادی که رطوبت گرفته اند را در کوره خشک کن با دمای 40 درجه به مدت سه ساعت قرار دهید تا روطوبت گرفته شود. ( دما های بالا تر سبب چسپیدن نوار ها به هم و تغییر شکل استوانه ای آن ها شود.)
دمای سینی را افزایش دهید.
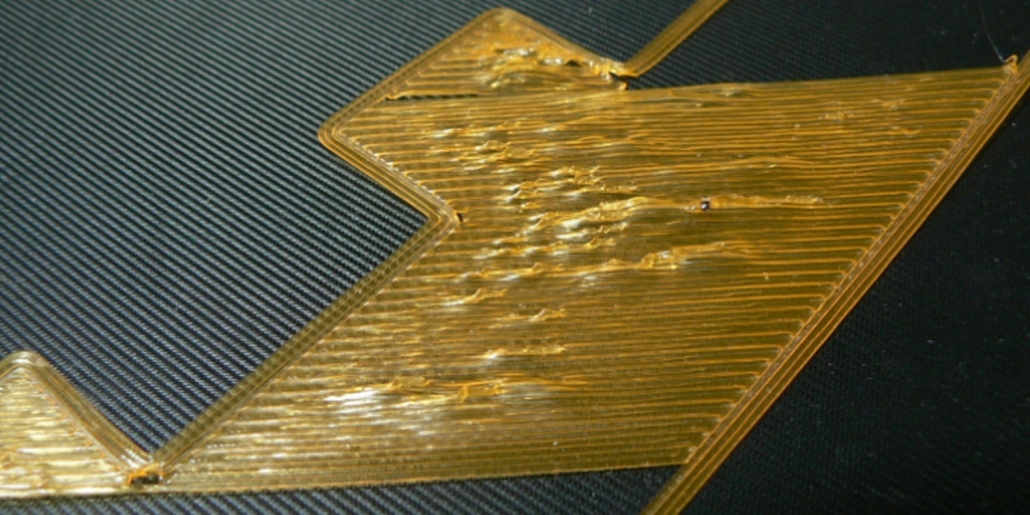
16. شکستن سطوح بالایی وپایینی
علت: نازک بودن بیش از اندازه و تراکم داخلی کم سبب می شود که قطعه بسیار شکننده شود.
راه حل: افزایش تعداد لایه ها باری سطوح بالا و پایینی (حداقل 2 تا 3 لایه) – افزایش تراکم داخلی
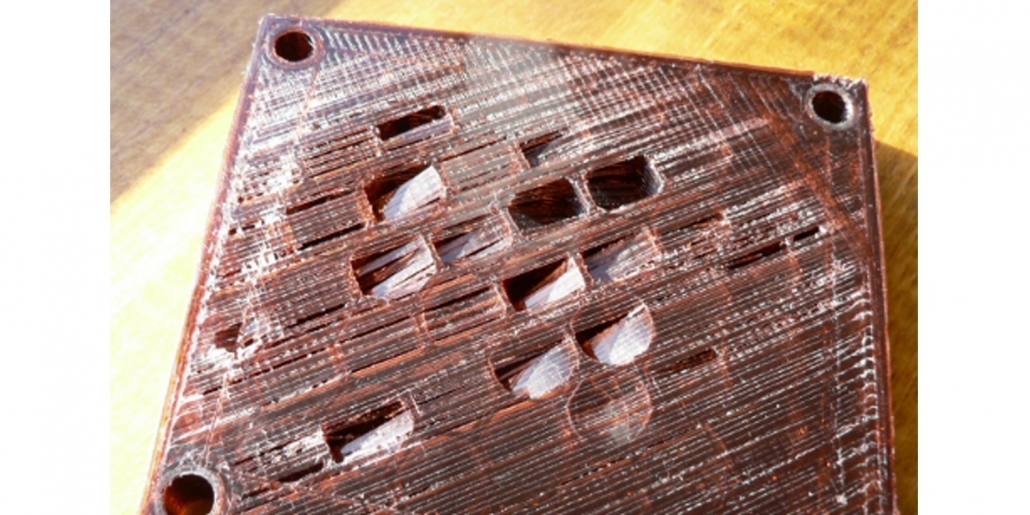
17. قسمت بالایی سوراخ ها می ریزد. در هنگام ساخت قطعه لایه های قسمت بالایی سوراخ سقوط می کنند.
علت: لایه ها برای بیش از اندازه موازی هستند. – تناسب صحیحی میان تزریق، دما و سرعت حرکت نازل وجود ندارد.
راه حل: کاهش میزان آویزان بودن این قسمت با تغییر شکل آن ها مثلا ایجاد شکلی مانند قطره آب تا یک دایره کامل یا استفاده از ساپورت.
اجازه دهید پرینت در این قسمت به آرامی و با سرعت کمتری انجام شود.
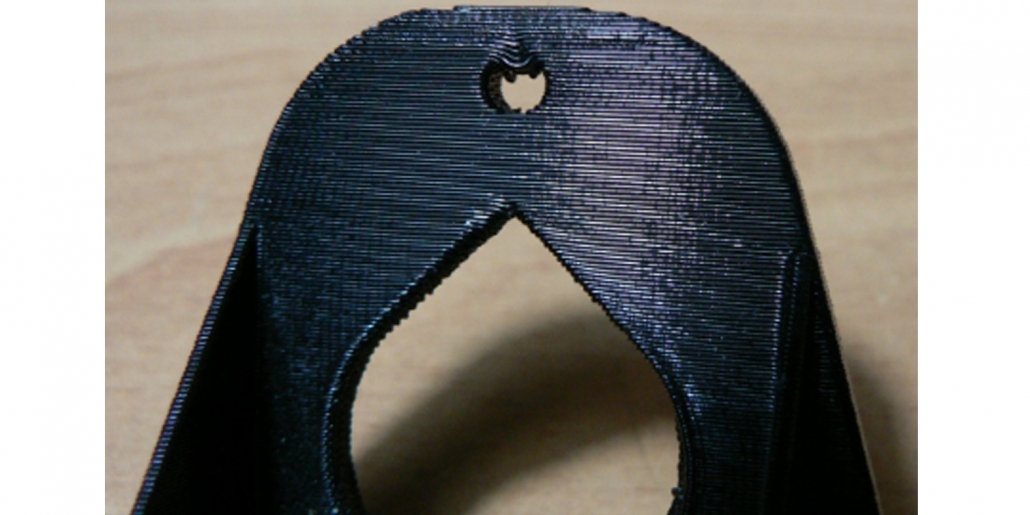
18. تغییر رنگ و شفافیت قطعه در طول آن
علت: تغییر تشکیل کریستال ها در طول زمان پرینت به علت تغییر دما و زمان سرد شدن و انجماد
راه حل: تغییر سرعت پرینت یا فن خنک کننده با توجه به سرعت پرینت و قرار گیری لایه ها.
کاهش دمای امستروژن و افزایش سرعت پرینت برای داشتن یک قطعه یک دست.
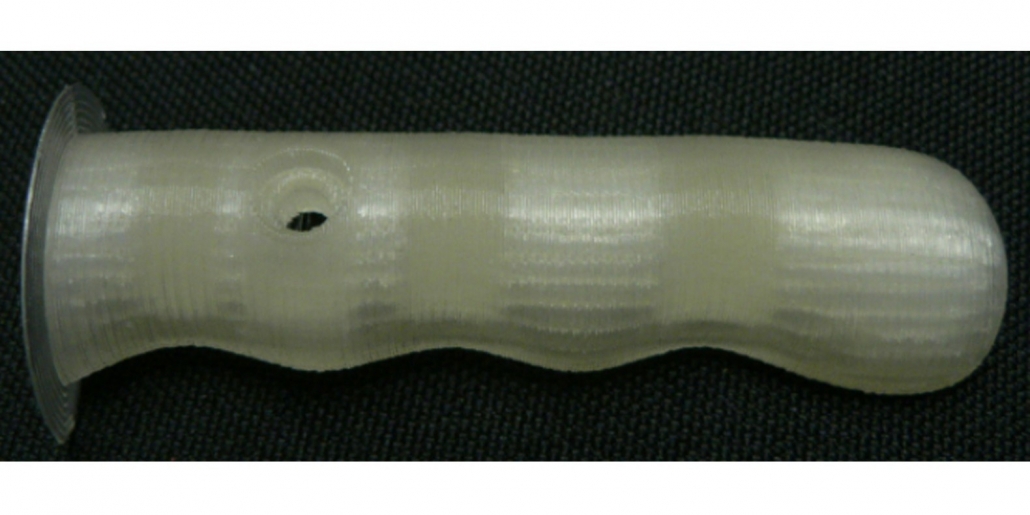
دیدگاهتان را بنویسید
می خواهید در گفت و گو شرکت کنید؟خیالتان راحت باشد :)