فرآیند قالبگیری تزریقی پودر فلزی (MIM)
در این مقاله قصد دارم فرآیند قالبگیری تزریقی پودر فلزی یا Metal Injection Molding که به اختصار به MIM معروف است را تو ضیح دهم.
قالبگیری تزریقی روشی کاربردی برای شکلدهی مواد است. درگذشته این فرآیند فقط برای شکلدهی ترموپلاستیکها استفاده میشد، اما فلزات و سرامیکها دارای خواص ویژه و برتری نسبت به ترموپلاستیکها ازجمله استحکام، سختی، خواص الکتریکی، مغناطیسی و حرارتی که پلیمرها فاقد آن بودند، هستند؛ بنابراین تکنولوژیهای تزریق به قالب و متالورژی پودر باهم ترکیب شدند و یک تکنولوژی جدید به نام قالبگیری تزریقی پودر فلز را به وجود آوردند.
ر این روش پودر فلزی مواد را با یک مجموعه ماده پلیمری مخلوط میکنند و یک توده قابل تزریق به وجود میآورند که آن را فیداستوک (Feedstock) مینامند. فیداستوک حاصل را توسط ماشینهای تزریق فلزی تزریق کرده تا قطعه خام (Green body) به دست آید. پس از تزریق، قطعه خام را چسبزدایی کرده و ماده پلیمری (چسب) موجود در قطعه را برطرف مینماید و سپس زینتر میکنند. مراحل فرآیند قالبگیری تزریقی پودر فلزی را نمایش میدهد.
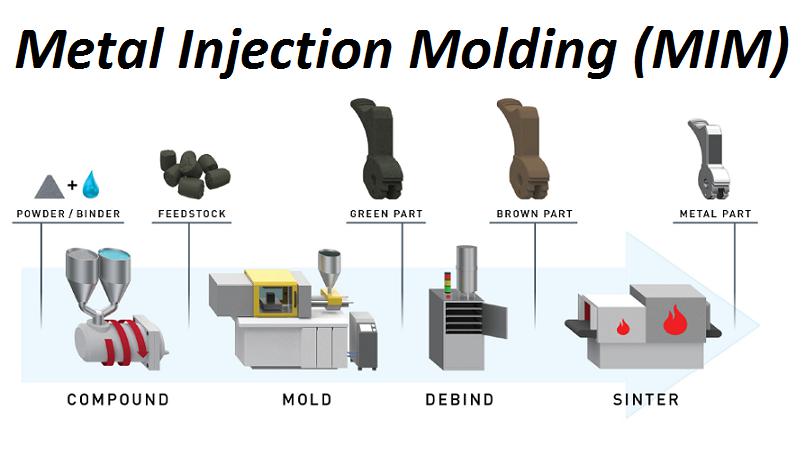
با توجه به شکل در این فرآیند ابتدا چسب پایه پلیمری یا بایندر (Binder) که ترکیبی از دو یا چند پلیمر پرکننده، و یک ماده سطحیساز (Surfactant) میباشد ساخته میشود. سپس در دمای کنترل شده، با درصدی از پودر آلیاژ فلزی ترکیب شده و همانطور که بیان شد فیداستوکبهدست میآید. خوراک تولید شده قابلیت تزریق درون قالب با شرایطی تقریبا مشابه فرآیند شرایط فرآیند تزریق پلاستیک را دارد. قالب قطعه که بسیار شبیه به قالب تزریق پلاستیک است، متناسب با قطعه نهایی ساخته شده و تحت شرایط ویژه تزریق، قطعهی خام را به وجود میآورد.
در مرحله بعد، بایندرزدایی (Debinding) به وسیله فرآیندهای حرارتی، شیمیایی، مواردحلالی و همچنین در برخی موارد به صورت فرآیندهای ترکیبی انجام میشود. در این مرحله بایندر را از پودر فلزی جدا کرده تا قطعهی خام بهدست آید. در مرحله بعد، بهمنظور رسیدن به چگالی موردنظر و استحکام مناسب، قطعه در کورهی مخصوص و تحت اتمسفر کنترل شده، حرارت داده میشود تا فرآیند زینتر رخ دهد. پس از این مرحله، قطعهی نهایی بهدست خواهد آمد و بدون هیچگونه عملیات تکمیلی، قابل استفاده خواهد بود.
در اين فرآیند تلاش ميشود تا چگالي قطعه به چگالي نظري آلیاژ نزديکتر شود و درنتيجه خواص مکانيکي مطلوب بهدست آید. تمامی قطعات بيومكانيكي در صنايع ظريف پزشكي، دندانپزشكي و جراحي كه نياز به استحكام، مقاومت در برابر خوردگي، شرايط سطحي و سازگاري محيطي خوب هستند و همچنین قطعات حساس الكترونيك و هوافضا توسط این فرآیند ساخته ميشوند.
فرآیند قالبگیریتزریقیپودرفلز، شباهت زیادی به فرآیند متالورژیپودر دارد و تفاوت عمده بین این دو فرآیند در ابعاد پودر، درصد افزودنی و شکلپذیری محصول میباشد. در متالورژیپودر متداول، از پودری با اندازه ذرات بین 100 تا 150 میکرومتر استفاده میشود و به منظور از بین بردن مشکل عدم پر شدن کامل قالب از ۵/۰ تا 1 درصد وزنی روانساز (Lubricant) استفاده میشود. این روانسازها در مرحله بایندرزدایی ازبین خواهند رفت. قطعهی نهایی در فرآیند متالورژی پودر معمولی، حدودا بین صفر تا 1 درصد حجمی انقباض خواهد داشت. محدودیت این فرآیند در شکلپذیری قطعههای ساده بوده و حداکثر چگالی قابل دسترس در این فرآیند، حدود 88 درصد خواهد بود که به همین دلیل خواص مکانیکی مطلوب از قطعه در این نوع فرآیندهای معمولی متالورژی پودر قابل دستیابی نمیباشد.
کنترل ماهیت تمام پارامترهای مرحلههای تزریق، بایندرزدایی و زینترینگ به عوامل مختلفی مانند: شکل، وزن قطعه، ابعاد و جنس مواد فلزی بستگی داشته و ضمن اینکه تمامی متغیرها به یکدیگر وابسته خواهد بود. بنابراین بهدست آوردن حالت بهینه مستلزم بکارگیری ترکیبی از روشهای شبیهسازی و کار تجربی برای هر قطعه در هر مرحله فرآیند خواهد بود. در پارامترهای تزریق، پراکندگی و یکنواختی پودر بسیار حائز اهمیت بوده و تغییرات کوچک در این پارامترها موجب تغییر در شرایط فیداستوک خواهد شد و بنابراین فرآیندهای بعدی را تحت تأثیر قرار خواهد داد.
تاریخچه فرآیند قالبگیری تزریقی پودر فلزی (MIM)
قالبگیری تزریقی پودر دنبالهرو اولین تحولات در قالبگیری تزریق پلاستیک بود. اولین محصولات قالبگیری تزریق پودر با ظهور قالبگیری تزریق پلاستیک بهصورت تصادفی ایجاد شدند. در سال 1930 میلادی همزمان در آلمان و ایالاتمتحده آمریکا، برای تولید شمعهای سوزنی سرامیکی، استفاده شدند که تمام این قطعات با تنوع گستردهی ابعادی همراه بودند. زیرساختهای تولید با ظهور تجهیزات کنترل فرآیند مانند قالب و کورههای زینتر که دارای چرخه تکرارپذیر و بدون نقص بودند، بهطور چشمگیری بهبود یافتند. در حدود 80% از ظرفیت تولیدات PIM به فلزات اختصاص دارد، که بهعنوان MIM شناخته میشود.
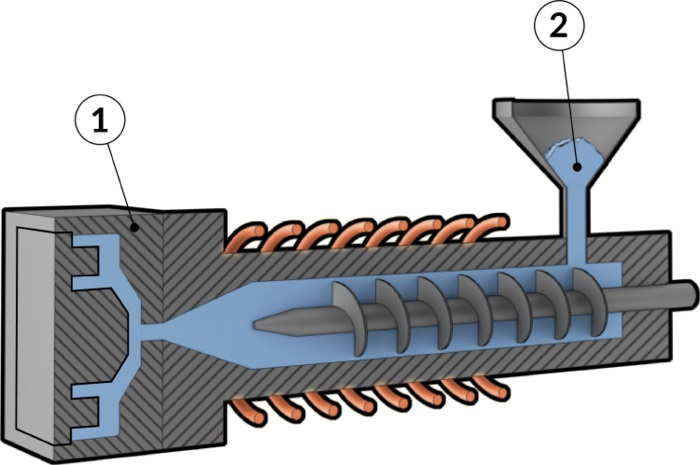
توجهها هنگامی جذب فرآیند MIM شد که این فرآیند جایزهی طراحی را در سال 1979 میلادی از آن خود کرد. از اواسط سال 1990 میلادی استفاده از مواد دیگر مثل پلیاتیلن گلیکول (Polyethylene glycol) جایگزین پارافین وکس (Paraffin wax) شد. بخاطر حلالیت آب در سیستم بایندری بدون استفاده از حلال است. بدین ترتیب قسمت شکل دادهشده را بهسادگی در آب غوطهور میکردند تا چسبهای بیشتری خارج شود و دانسیته محصول افزایش یابد.
بنابراین، فرآیند MIM بر اساس تکنولوژی قالبگیری پلاستیک برای شکلدهی گرانولهپودر- پلیمر به شکل موردنظر است، بعد از قالبگیری پلیمر حذفشده و ذرات بهوسیلهی زینترینگ در دمای بالا متراکم میشوند و اغلب در مواجهه با روش سنتی فشار-زینتر در متالورژی پودر و ریختهگری دقیق، قطعه نهایی با خواص مکانیکی مطلوبتری را ایجاد می کند. فرآیند MIM با دیگر روشهای شکلدهی فلزات مانند ریختهگری، ماشینکاری، فشردهسازی ایزواستاتیک سرد و ریختهگری نواری (Tape Casting) قابل رقابت میباشد. این روش بر محدودیتهایی مانند محدودیت شکلدهی و فشردهسازی در متالورژی پودر متداول، هزینه و بهای بالای ماشینکاری، محدودیت تولید در فرآیند پرسکاری ایزواستاتیک و ریختهگری نواری و عیوب و محدودیتهای تغییر ابعادی در ریختهگری متداول غلبه کرده است.
فرآیندها و مراحل MIM
در روش قالبگیری تزریقی پودر، مواد را با یک مجموعه ماده پلیمری مخلوط میکنند و یک توده قابل تزریق به وجود میآورند که آن را فیداستوک یا همان لقمه اولیه مینامند. فیداستوک حاصل را توسط ماشینهای تزریق تزریق کرده تا قطعه خام (Green body) به دست آید. پس از تزریق، قطعه خام را چسب زدایی کرده و ماده پلیمری (چسب) موجود در قطعه خارج میشود. سپس قطعه بهمنظور افزایش استحکام و خواص مکانیکی توسط کورههایی با اتمسفر کنترلشده، زینتر میگردد.
بهصورت عمومی مطابق شکل فرآیند MIM شامل 4 مرحله است: مخلوط کردن پودر و بایندر (چسب) برای آمادهسازی فید استوک، تزریق فیداستوک به درون قالب، بایندرزدایی بهمنظور حذف کردن قسمت قابلتوجهی از چسب و در نهایت زینتر کردن پودر به منظور نفوذ و دستیابی به قطعه نهایی میباشد.
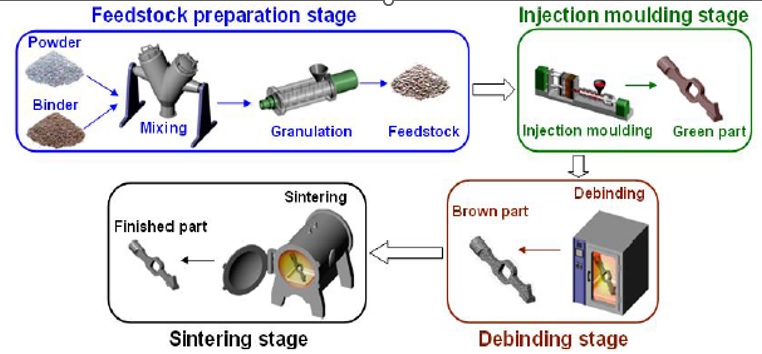
قالبگيري مستلزم گرمايش و فشارگذاري همزمان خوراك است. دستگاه قالبگيري، خوراك را تا دمايي حدود ۱1۰ تا C°25۰ گرم ميكند و سپس قالبگيري بسته به نوع قالب و وزن قطعه نهایی در حدود 3 تا 50 ثانیه روي ميدهد. با سيلان پودر در قالب، سرمايش خوراك همراه با افزايش میزان گرانروي آن رخ ميدهد.
افزايش مقاومت به سيلان در هنگام پركردن قالب منجر به افزايش فشار لازم براي پركردن محفظه ميشود. بيشترين فشار قالبگيري به هندسه قالب، بایندر و مشخصههاي پودر بستگي دارد. درنتيجه، دما و فشار متغيرهاي كنترلي اصلي در فرآیند قالبگيري تزریق پودر به شمار ميآيند. در محدوده دمایی ۱1۰ تا C°25۰ در هنگام تزریق انبساط گرمايي بایندر بسيار بيشتر از پودر است، از اين رو، در هنگام گرمايش، حجم اشغال شده توسط بایندر نسبت به پودرفلز افزايش يافته و در نتیجه درصد پودر جامد و گرانروي خوراك را کاهش میهد. علاوه بر این پليمر نیز با افزايش دما، سيلان آسانتري از خود نشان ميدهد. اين دو عامل با هم تركيب ميشوند تا گرانروي فعال شده با گرما تأمين شود.
بعد از فرآیند قالبگیری قطعه فشرده شده به آهستگي بسته به نوع فیداستوک تا دماي حدود C°۶۰۰ در هوا يا تحت اتمسفر کنترلی حرارت داده ميشود تا در نتیجه بایندر تجزيه شود. راه ديگر بایندر زدایی غوطهورسازي قطعه شكل گرفته در حلالي است كه اجزاي بایندر را حل ميكند. استفاده از نوع حلال در این مرحله کاملاً به ترکيب خوراک اولیه و استفاده از گرما و همچنین واکنش بین بایندر و پودر فلزي بستگي دارد. مرحله بعدي زینترینگ است كه ميتواند مستقيماً در چرخه بایندرزدایی و به صورت پیوسته با این مرحله انجام شود. زینترینگ، پيوندهاي ميانذرهاي قوي ايجاد ميكند و فضاي خالي را به وسيله چگالش پودر حذف ميكند.
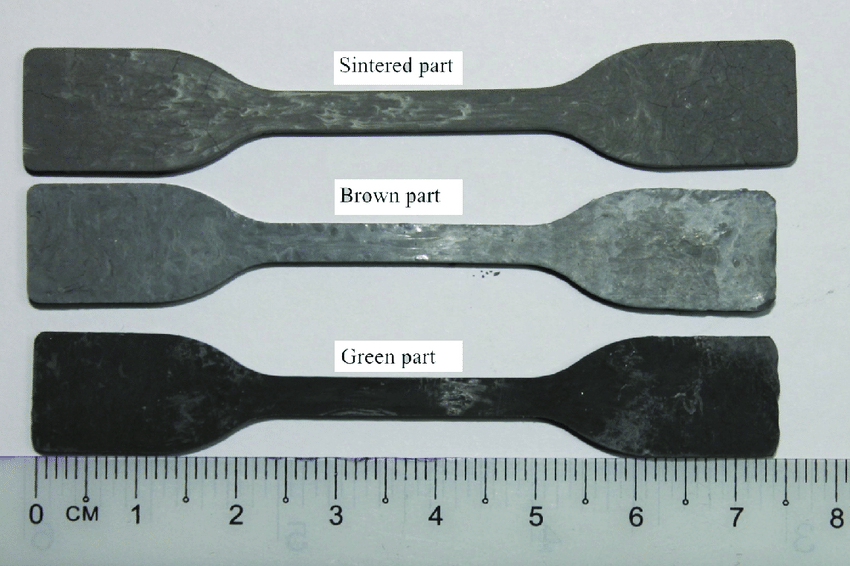
فرآیند قالبگیریتزريقیپودرفلز براي ساخت قطعههایی از جنس فولاد زنگنزن با ابعاد بسيار کوچک و اشکال پيچيده، بسيار با ارزش است. تمامی قطعههای بيومكانيكي در صنايع ظريف پزشكي، دندانپزشكي و جراحي كه نياز به استحكام، مقاومت در برابر خوردگي، شرايط سطحي و سازگاري محيطي دارند و قطعههای حساس الكترونيك و هوافضا از اين فرآیند ساخته ميشوند. در برخي از مقالهها هم از این فرآیند بهعنوان بهترين فرآیند براي ساخت کامپوزيتهاي داراي الياف ناپيوسته و مواد بايومتريال نام برده شده است.
چهار دلیل اصلی انتخاب قالبگیریتزریقیپودرفلز عبارتند از :
الف) پیچیدگی: امکان ساخت قطعه پیچیده
ب) ابعاد: بطور کلی محدوده وزنی قطعهها مناسب برای این فرآیند، از 1/0 تا ۲۵۰ گرم میباشد. مناسبترین ضخامت برای دیوارهها، بین ۱۳ تا 7/12 میلیمتر است. با توجه به محدودیت حرکت سیال، فاصله بین دورترین نقطهی قطعه تا محل دهانه ورودی مواد نباید بیشتر از ۱۰۰ میلیمتر باشد..
ج) تیراژ تولید: این فرآیند برای تولید قطعههای بین ۱۰۰ هزار تا دومیلیون قطعه توجیه اقتصادی دارد. برای تولید قطعههایی با تیراژ بیشتر، امکان طراحی و ساخت قالب با حفرههای بیشتر وجود خواهد داشت.
د) خواص نهایی: دستیابی به چگالی تئوری ماده و خواص مکانیکی بالا بسیار ایدهآل میباشد. تقریباً محدودیتی برای دستیابی به آلیاژهای فلزی در این فرآیند، وجود ندارد. شکل نمونههایی که با روش قالبگیریتزریقیپودرفلز در صنایع مختلف را نمایش میدهد.
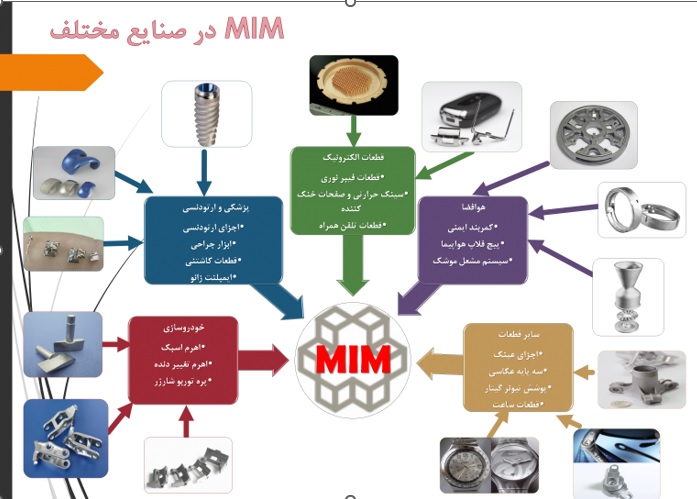
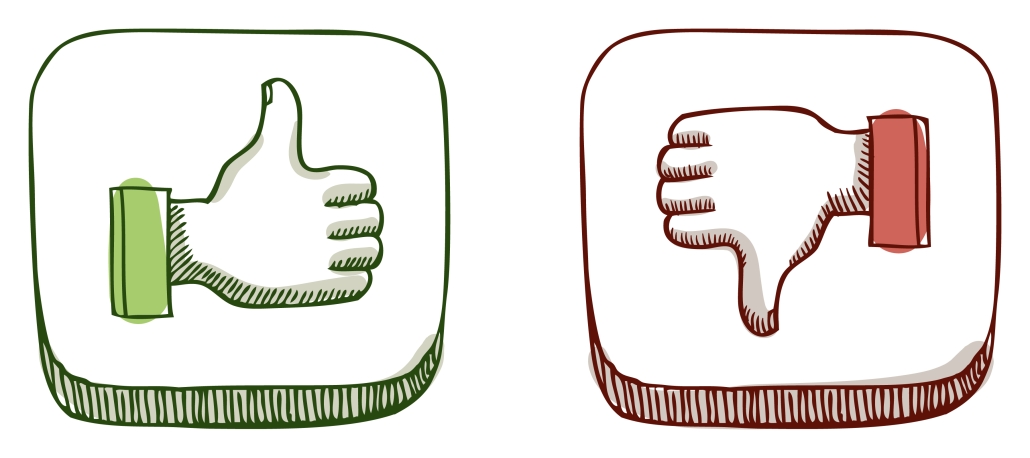
ویژگیهای فرآیند MIM، منجر به کاربرد گسترده این روش نسبت به سایر روشهای تولید در بسیاری از قطعات شده است. مزایای این فرآیند به شرح زیر میباشد:
دسترسی به دامنهی گستردهای از آلیاژها وکامپوزیتها.
تولید نمونههایی با شکلهای پیچیده و تیراژ انبوه.
قابلیت دامنهی وسیعی از شکل و طراحی.
کاهش هزینهها بهطور قابلتوجه، مانند کاهش هزینهی نیروی انسانی.
بهای تولید مناسب جهت تولید قطعات در حجم متوسط تا زیاد.
توانایی ایجاد فرآیند بهصورت کاملاً اتوماتیک.
تولید قطعات با سطح نهایی بسیار خوب و مناسب و درنتیجه حذف مرحلهی ماشینکاری.
توانایی حذف بعضی از فرآیندهای کاری و درنتیجه کاهش هزینههای تولید.
مناسب برای تولید قطعات پیچیده مانند کلافها، زبانهها، رزوه و لولهها با نسبت طول به قطر بالا است.
تولید قطعات با چگالی بالا (بین 95 تا 98 درصد چگالی تئوری) و خصوصیات فوقالعاده مانند استحکام، مقاومت خوردگی و خواص مغناطیسی بهتر نسبت به دیگر روشهای تولید دارا میباشد. شکل زیر مقایسه میزان تولید نسبت به پیچیدگی شکل قطعات در روشهای تولید مختلف را نمایش میدهد.
همچنین فرآیند MIM دارای محدودیتهایی نیز میباشد که در زیر بیانشدهاند:
- تهیه مادهی اولیه مورد استفاده در این روش (پودرهای فلزی در حد میکرومتری) نسبتاً هزینهبر است.
- نیاز به دستگاههای گرانقیمت اولیه دارد، بهعبارتدیگر هزینه سرمایهگذاری اولیه بالا است.
- برای تولید نمونههای ساده و با تقارن محوری، این روش در مقایسه با سایر روشهای تولید مقرون بهصرفه نیست.
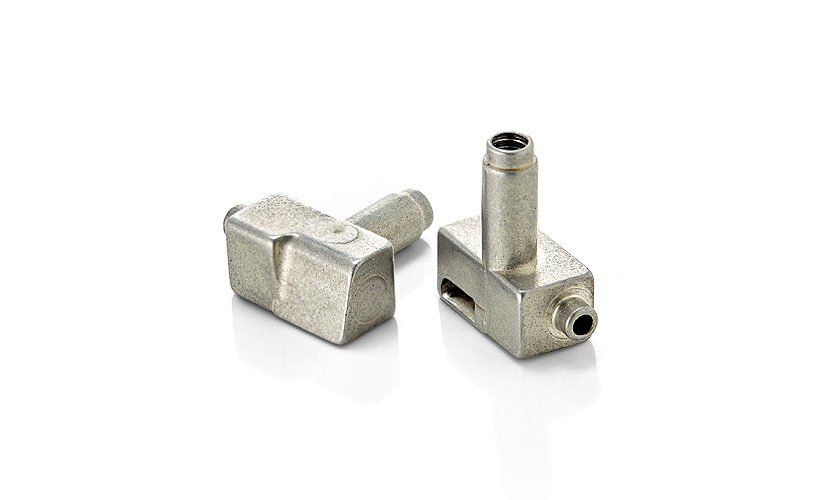
منابع و مراجع
[1] ژرمن، رندال. متالورژی پودر و مواد ذره ای. مجتبی ناصریان ریابی. ترجمه علی حایریان اردکانی، مجتبی ریابی، محمدحسین همتی و بابک مشایخی. تهران: انتشارات دانشگاه صنعتی امیرکبیر 1387.
[2] Heaney, Donald F., Handbook of metal injection molding, Woodhead Publishing Limited, Philadelphia, 120-131, 2012.
[3] Kong, Xiangji, Development and characterization of polymer- metallic powder feedstocks for micro-injection molding, Ph. D. thesis, Université de Franche-Comté, 1220-1231, 2013.
[4] Ali Dehghan-Manshadi, Michael Bermingham, Metal Injection Moulding of Titanium and Titanium Alloys: Challenges and Recent Development, Powder Technology, 0032-5910, 2017.
[5] Berginc, Bostjan, Xing. ZHENG Zhen, Numerical simulation of tungsten alloy in powder injection molding process, Advanced Powder metallurgy, 1209-1215, 2008.
[6] X. Kong, Devolopment and characterization of polymer-metallic powder feedstock for micro-injection molding, Powder Technology, 2011.
[7] ZHENG, Zhen-xing, 2008, Numerical simulation of tungsten alloy in powder injection molding process, Advanced Powder metallurgy, 18: 1209-1215, 2014.
[8] S. N. O.D.Neikov, V.G.Gopiekol, V.Frishberg, Handbook of NonFerrous Metal Powders: Technologies and Applications, 22: 1606, 2009.
[9] Kate, Kunal H., Feedstock properties and injection molding simulations of bimodal mixtures of nano scale and micro scale, Powder Technology, 39:6887–6897, 2013.
[10] Lin, Dongguo, Development of Powder Injection Molding Process for Fabrication of Glass Component, University of Science and Engineering, Pohang, Korea, 790-784, 2016
مراجع بیشتر برای مطالعه
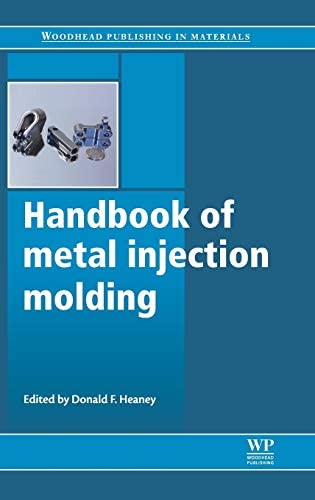
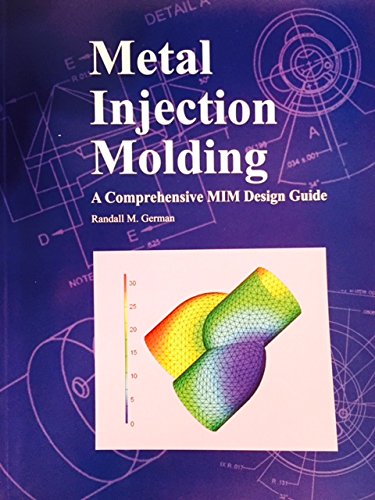
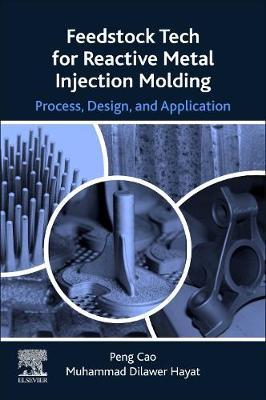
بازتابها و دنبالکها
[…] که در مقاله دیگری با همین عنوان ” قالبگیری تزریقی پ… […]
دیدگاهتان را بنویسید
می خواهید در گفت و گو شرکت کنید؟خیالتان راحت باشد :)