متالورژی پودر و کاربردهای صنعتی آن
مقدمه
متالورژی پودر روشی برای ساخت و تولید قطعات فلزی و سرامیک است که اساس آن بر فشردن پودر اولیه مواد به شکل مورد نظر و سینترینگ در درجه حرارتهای زیر نقطه ذوب میباشد. متالورژی پودر بخشی کوچک ولی بسیار مهم از صنایع فلزی و سرامیکی به شمار میآید
اولین کاربرد متالورژی پودر برای تولید پلاتین با دانسیته بالا بود که در قرن 19 میلادی صورت گرفت چون در آن زمان امکان ذوب پلاتین به دلیل نقطه ذوب بالا وجود نداشت. در اوایل قرن بیستم فلزهای دیر گدازی مانند تنگستن و مولیبدن توسط روش متالورژی پودر شکل داده شدند. کاربیدهای سمانیت و یاتاقانهای برنزی متخلخل نسل بعدی قطعات متالورژی پودر به حساب میآیند. بدین ترتیب قطعات متالورژی پودر در انواع صنایع مانند: لوازم خانگی، اسباب بازی سازی و الکترونیک کاربرد پیدا نمود. آخرین کاربردهای قطعات متالورژی پودر در صنایع خودرو سازی میباشد که موازی با رشد صنایع اتومبیل سازی رشد نمود و به صورتی که امروزه بقای صنعت متالورژی پودر در کشورهای صنعتی بسیار وابسته به صنعت خودرو سازی میباشد.
در سالهای ۱۹۵۰-۱۹۶۰ میلادی روشهای نوینی مانند: فُرج پودرو ایزو استاتیک گرم در صنعت متالورژی پودر بکار گرفته شد. این روشها با تولید قطعات با دانسیته بالا توان رقابتی قطعات متالورژی پودر را افزایش دادند. گرچه روش متالورژی پودر امکانات ویژهای را جهت تولید بعضی قطعات خاص فراهم ساختهاست، که تولید آنها از طریق روشهای دیگر غیر ممکن یا بسیار مشکل میباشد ولی زمینههایی که باعث فراگیر شدن استفاده از این روش گردیدهاست، عبارتاند از:
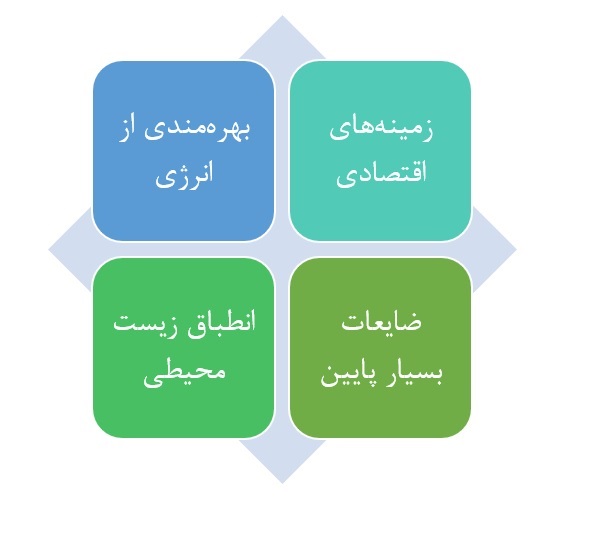
با وجود اینکه از نظر تاریخی متالورژی پودر جز قدیمیترین روشهای شکل دادن فلزات است، اما تولید در مقیاس تجاری با این روش، از جدیدترین راههای تولید قطعات فلزی است. در دوران باستان از روشهای متالورژی پودر برای شکل دادن فلزاتی با نقطه ذوب بالا مورد استفاده قرار میگرفت.
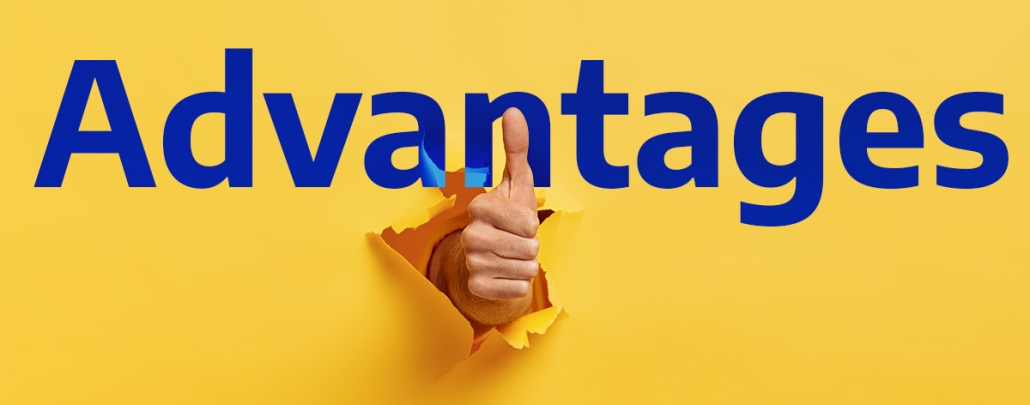
مزایای متالورژی پودر
روش متالوژي پودر امكانات ويژهاي دارد كه برجسته ترين آن ها به شرح زير میباشد:
- به كارگيري عناصر آلياژ نشدني
برخي فلزات كه آلياژ آنها از ويژگي هاي منحصر به فردي برخوردار است ولي توليد آنها در فاز مذاب (ريخته گري) غير ممكن است با به كارگيري متالورژي پودر قابل توليد میباشند. اين فلزات عناصر مخلوط نشدني ناميده ميشوند. از جمله اين مواد ميتوان به آلياژ نقره و نيكل اشاره كرد كه براي ساخت قطعات فلزی كليدهاي برق به کارگرفته ميشود[1,2].
- ساخت قطعات خود روغنكار
اين روش توليد براي ساخت بوشهاي خود روغنكار مورد استفاده قرار ميگيرد قطعات پس ازتفجوشي با روغن اشباع شده و در حين كارعمل روغنكاري سطوح تماس با روغن تزريق شده در قطعه عملي ميگردد .
- استفاده از فلزات دير گداز
فلزاتي كه ريختهگري آنها به دليل نقطه ذوب بالا با اشكال روبروست به روش متالورژي پودر شكل داده ميشوند. بهترين مثال در اين مورد رشتههاي لامپ روشنايي میباشد. اين رشتهها بايد داراي نقطه ذوب و ويژگيهاي الكتريكي مناسبی باشند. مناسبترين ماده براي ساخت این مواد تنگستن است که نقطه ذوب آن در حدود 3400 درجه سانتي گراد میباشد. پودرتنگستن نخست با روش متالورژي پودر به شكل شمش تبدیل شده و سپس به روشهاي آهنگري و كشش سيم به رشته مورد نظر تبديل ميشود.
- فرایند سبز
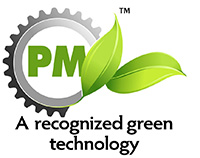
درجدول زیر قایسه انواع روش های تولید مواد در مقایسه با روش متالورژی پودر آورده شده است.
روش تولید | مزایا در مقایسه با متالورژی پودر | ضعفها در مقایسه با متالورژی پودر |
شکل دهی سرد | بالاتر بودن استحکام، پرداخت سطحی خوب | دقت پایین، کوتاهتر بودن عمر ابزارها، محدود بودن مواد |
حدیده کاری | تولید قطعات با طول زیاد، صافی سطح، سرعت تولید | ثابت بودن سطح مقطع قطعه، پایینتر بودن دقت، انرژی مصرفی بالا، بدون پله بودن قطعات، کوتاهی عمر ابزارها |
پرس ورق | تخت بودن سطح، دقت بالا، آهنگ تولید بالا، تولید قطعات دارای سطوح بزرگ، موقعیت دقیق نقشها | محدود بودن تنوع مواد، ضایعات، خشن بودن لبهها، مشکل بودن ایجاد نقش در اندازههای کوچک |
ریخته گری | گسترده بودن دامنه کاربرد، امکان تولید قطعات کوچک تا بزرگ، پایین بودن هزینههای آماده سازی، پایین بودن هزینه ابزار | برای دیر گدازها مناسب نیست، وجود ترشحات فلزی چسبیده به سطح، وجود خط جدایش، ناهمگنی، تخلخل، نقایص و نیاز به بازیابی مواد راهگاها و مجاری مذاب رسانی |
شکل دهی گرم | بالا بودن خواص مکانیکی، تولید قطعات بزرگ و پیچیده، سرعت تولید بالا، سهولت جریان ماده | ترشحات فلزی و ضایعات، کنترل ضعیف ابعادی، ناخالصیهای غیر فلزی و نقایص فنی، سایش سریع ابزارها |
ماشین کاری | قابلیت استفاده برای اندازههای متفاوت، دقت بالا، کوتاه بودن زمان مرده، عدم نیاز به ابزار شکل دهی، قابلیت تولید در حجم کم | ضایعات زیاد، بهره وری کم، غیر یکنواختی خواص، هزینه زیاد، هزینه بالای نیروی انسانی |
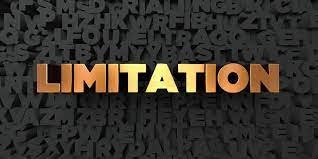
محدودیتهای متالورژی پودر
به طور کلی مهمترین محدودیت های ناشی از فرآیند متالورژی پودر در تولید قطعات مختلف به صورت زیر میباشد [1]:
- هزینه بالای تولید پودر.
- خواص مکانیکی پایین تر نسبت به قطعاتی که به روشهای دیگر تولید شده اند (به علت وجود تخلخل در قطعه).
- محدودیت از لحاظ وزن وابعاد قطعه.
- هزینه بالا برای سینتر کردن قطعات (نیاز به کوره با گاز محافظ).
- عدم یکنواختی خواص مکانیکی در قطعه.
- هزینه بالای بکارگیری پرس وقالب.
- مشکلات تکنولوژیکی مثل چسبیدن پودر به قالب یا جنس قالب.
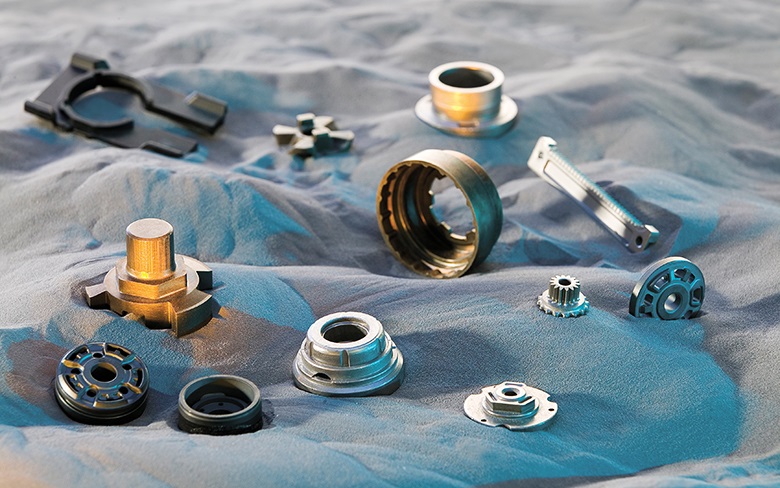
کاربرد قطعات متالورژی پودر
فرآیند متالورژی پودر کاربرد وسیعی در صنایع مختلف دارد که از مهمترین آن به موارد زیر میتوان اشاره کرد:
- تولید مغناطیسها: مانند مغناطیسهای فریتی.
- صنعت خودرو سازی: مانند چرخدنده ها.
- تولید یاتاقانها از آلیاژهای مس وسرب.
- ساخت کامپوزیتها مانند: کامپوزیت مس-گرافیت.
- سرمتها مانند: Al2O3-Ni ،Al2O3-Cr و….
- قطعات ابزار مانند: تنگستن و کاربید-کبالت برای ابزار سایشی.
- صافی یا فیلترها.
- سوپرآلیاژها: مانند آلیاژهای پایه نیکل که در مقابل خزش وخوردگی مقاومت خوبی دارند و در ساخت پره توربین بکار میرود.
- مواد دیرگداز: مانند رشته لامپ که از جنس تنگستن میباشد.
- صنایع الکترونیکی: مانند کنتاکت کلیدها وکنتاکتورها
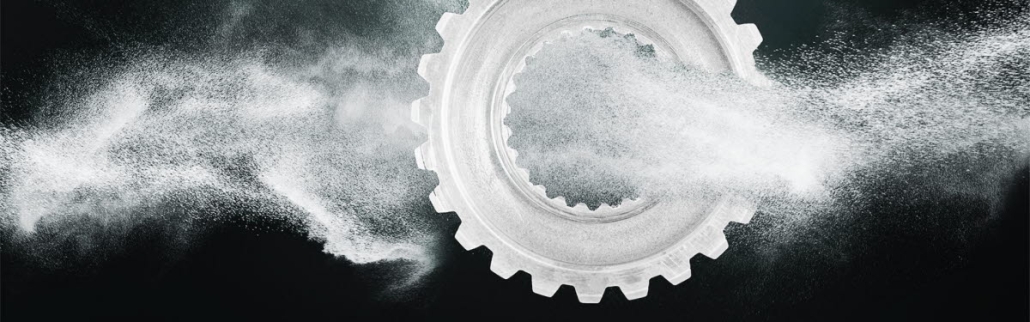
یکی از محبوبترین روشهای متالورژی پودر ، قالبگیری تزریقی پودر فلز است؛ قالبگیری تزریقی روشی کاربردی برای شکلدهی مواد است. درگذشته این فرآیند فقط برای شکلدهی ترموپلاستیکها استفاده میشد، اما فلزات و سرامیکها دارای خواص ویژه و برتری نسبت به ترموپلاستیکها ازجمله استحکام، سختی، خواص الکتریکی، مغناطیسی و حرارتی که پلیمرها فاقد آن بودند، هستند؛ بنابراین تکنولوژیهای تزریق به قالب و متالورژی پودر باهم ترکیب شدند و یک تکنولوژی جدید به نام قالبگیری تزریقی پودر فلز را به وجود آوردند [3].
در این روش پودر فلزی مواد را با یک مجموعه ماده پلیمری مخلوط میکنند و یک توده قابل تزریق به وجود میآورند که آن را فیداستوک مینامند. فیداستوک حاصل را توسط ماشینهای تزریق فلزی تزریق کرده تا قطعه خام به دست آید. پس از تزریق، قطعه خام را چسبزدایی کرده و ماده پلیمری (چسب) موجود در قطعه را برطرف مینماید. قطعه چسبزدایی شده را بهمنظور افزایش استحکام و خواص مکانیکی توسط کورههایی با اتمسفر کنترلشده، سینتر میکنند [4]. در شکل بالا مراحل فرآیند قالبگیری تزریقی پودر فلزی را نمایش میدهد.
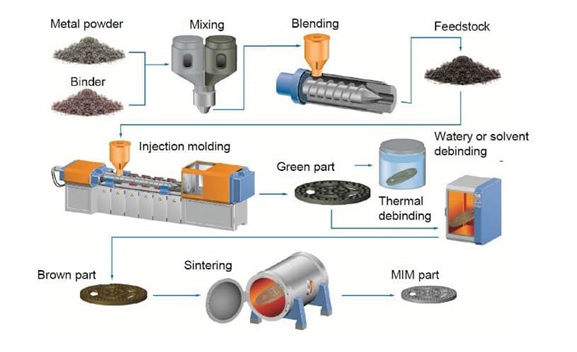
در شکل زیر، مقایسهی فرآیند قالبگیریتزریقیپودرفلزی با فرآیندهاي معمول از ديدگاه هزينهی تمامشده سنجيده شده است كه تمایل به خدمت گرفتن اين فناوري را با توجه به سوددهي و بهرهوري بالاي آن توجيه ميکند[6].
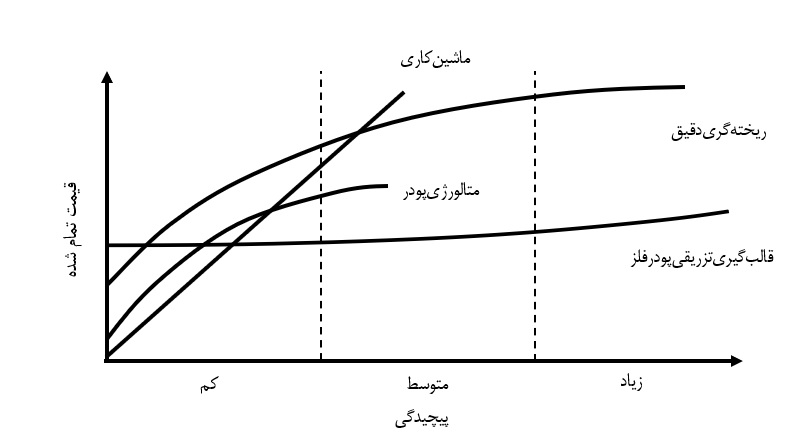
در این ویدیو به طور کامل فرایند متالورژی پودر را توضیح می دهد.
که در مقاله دیگری با همین عنوان ” قالبگیری تزریقی پودر فلز یا MIM” به بررسی آن خواهیم پرداخت.
منابع و مراجع
[1] ژرمن، رندال. متالورژی پودر و مواد ذره ای. مجتبی ناصریان ریابی. ترجمه علی حایریان اردکانی، مجتبی ریابی، محمدحسین همتی و بابک مشایخی. تهران: انتشارات دانشگاه صنعتی امیرکبیر 1387.
[2] Heaney, Donald F., Handbook of metal injection molding, Woodhead Publishing Limited, Philadelphia, 120-131, 2012.
[3] Kong, Xiangji, Development and characterization of polymer- metallic powder feedstocks for micro-injection molding, Ph. D. thesis, Université de Franche-Comté, 1220-1231, 2013.
[4] Ali Dehghan-Manshadi, Michael Bermingham, Metal Injection Moulding of Titanium and Titanium Alloys: Challenges and Recent Development, Powder Technology, 0032-5910, 2017.
[5] Berginc, Bostjan, Xing. ZHENG Zhen, Numerical simulation of tungsten alloy in powder injection molding process, Advanced Powder metallurgy, 1209-1215, 2008.
[6] X. Kong, Devolopment and characterization of polymer-metallic powder feedstock for micro-injection molding, Powder Technology, 2011.
منابع بیشتر برای مطالعه
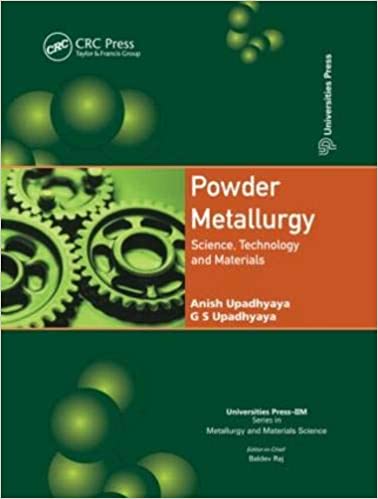
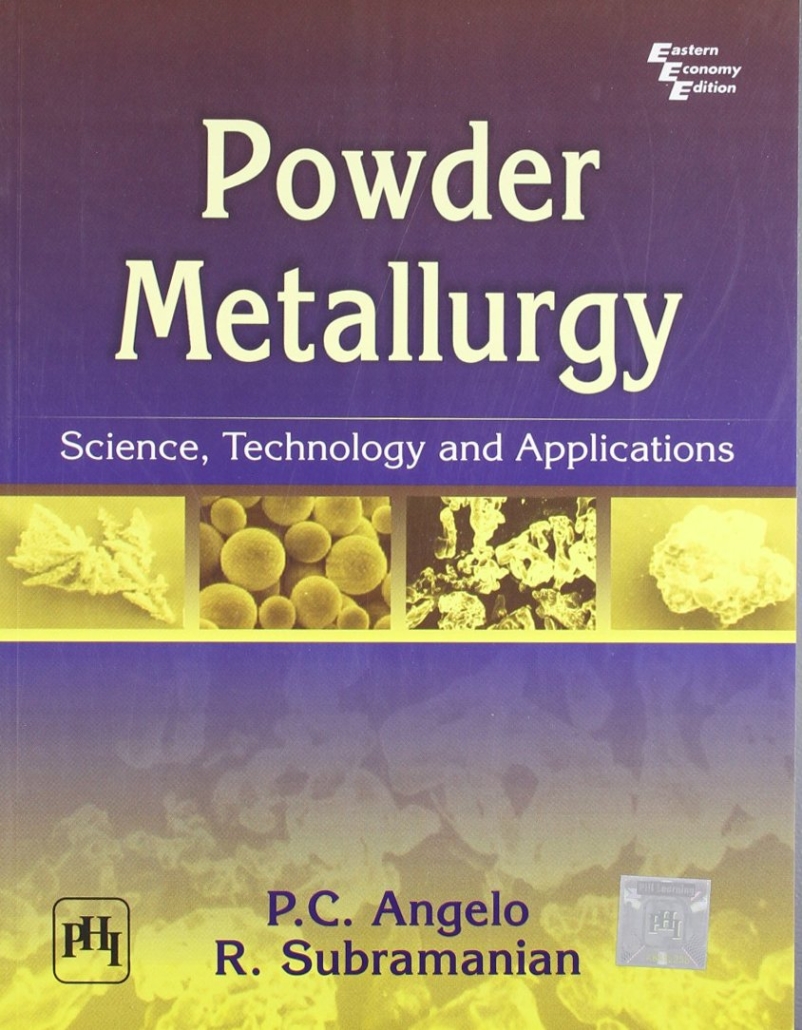
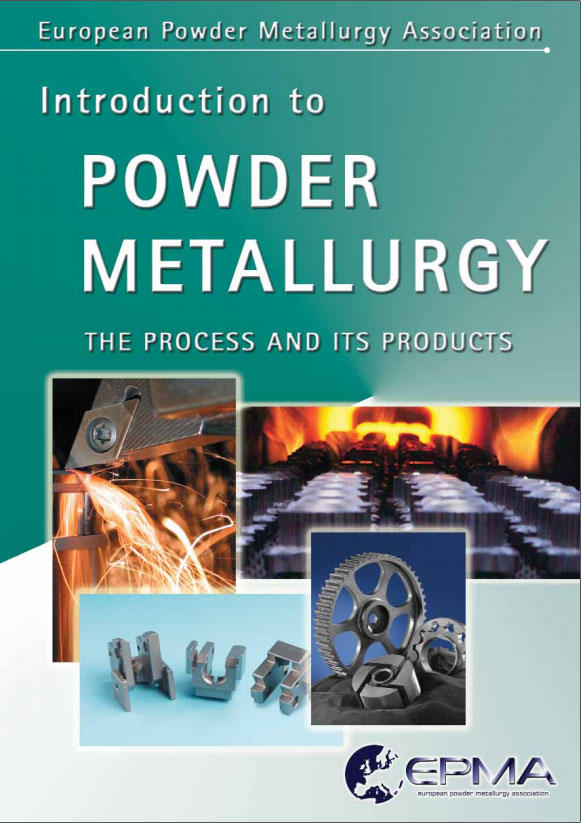
بازتابها و دنبالکها
[…] قالبگیریتزریقیپودرفلز، شباهت زیادی به فرآیند متالورژیپودر دارد و تفاوت عمده بین این دو فرآیند در ابعاد پودر، درصد […]
دیدگاهتان را بنویسید
می خواهید در گفت و گو شرکت کنید؟خیالتان راحت باشد :)